Asphalt is a popular choice for roadway construction. It’s relatively inexpensive compared to other paving materials and is known for its durability.
Proper grading and drainage are vital to the longevity of asphalt pavement. It is also important to choose a contractor with experience working with your specific type of road or driveway. Contact Asphalt Paving Charleston SC now!
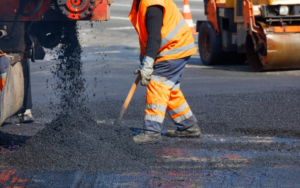
Before you can install new asphalt, the old surface needs to be removed. This is done with heavy machinery like bobcats and forklifts, creating a clean slate from which to start. Once the area has been stripped, any soft areas need to be fixed. This can be done by either excavating to the proper depth and re-grading or by using geo-grids. These methods will provide a stronger foundation for the asphalt pavement, increasing its lifespan.
The next step is preparing the sub-base and base course. This includes adding crushed stone, gravel, recycled asphalt, or concrete. It acts as a frost barrier in cold climates, and provides a strong foundation for the asphalt that will be placed on top of it.
This layer also helps to distribute traffic and environmental load in a way that reduces rutting. It requires a high stiffness, adequate fatigue resistance, and a good level of shear strength to prevent failure in the long term. The base course is usually made of a dense graded mix, which uses larger aggregates that “float” in a matrix of mastic consisting of asphalt cement and screenings/fines.
Once the base is prepared, it’s time to apply a binder layer. This is a large aggregate mixed with oil that will provide the strength of your asphalt surface. There are many different types of asphalt binder available, including modified binders that contain additives to improve performance. The type of binder used will depend on the climate and the traffic load expected to be applied to the asphalt.
After the binder is laid, the surface asphalt can be added. This is the jet-black finish that we are all familiar with on roadways, parking lots, and driveways. This is created by applying an asphalt mix that contains bitumen (binding agent), oil, and sand.
After the asphalt is laid, it is important to keep traffic off of it until it has cured. This is a process that can take up to a year, and it’s crucial for the longevity of your asphalt surface. Effective traffic management and appropriate signage can help ensure that all traffic is kept off the newly paved surface during this period.
Laying
Asphalt pavement isn’t just poured on the ground. It has layers underneath it that are carefully designed and constructed to ensure the pavement can withstand heavy loads, inclement weather, and environmental stresses. Understanding these different components can help you appreciate the complexity and engineering that goes into building quality asphalt surfaces.
To begin laying your new asphalt surface, a contractor must remove any existing material. This can be done using a variety of tools, depending on the size of the area to be removed. Heavy machinery like jackhammers, bulldozers, and excavators may be used to break up and remove the old surface.
Once the surface is clean, a grader can shape the new base layer to achieve a desired slope and profile. This can help reduce water runoff and rutting, both common issues that affect asphalt longevity. The sub-base layer is installed next, which is a strong aggregate base that helps the asphalt pavement resist heaving and rutting during the freeze-thaw cycle of winter.
A binder course is then laid over the base, a layer that adds strength and stability to the asphalt surface. It is made of larger aggregate mixed with asphalt binder to form a cohesive and durable layer. The thickness of the binder course varies, depending on the expected traffic load.
Finally, the surface asphalt is laid over the binder and graded to create a smooth, jet-black finish that pedestrians are familiar with seeing on roadways and parking lots. It can be a mix of recycled and reused materials, which helps promote sustainability in the industry.
Once the top surface of your asphalt is paved, you can prevent it from getting worn down and damaged by applying a seal coat to protect it from UV rays, water, and chemicals. This can extend the life of your asphalt for years to come.
To keep your asphalt surface looking fresh and avoiding costly repairs, it’s important to follow the best practices for maintenance. This includes routine crack sealing, which can help prevent moisture from affecting the sub-grade and surface asphalt layers.
Compaction
The asphalt compaction process locks the asphalt-coated aggregate particles together to achieve stability and resistance to deformation (or rutting). Compaction also reduces permeability for long-term durability. The ability of the pavement structure to withstand traffic stresses is dependent on both the thickness of the pavement and the level of compaction achieved in the construction process. Inappropriate compaction of an asphalt mixture will result in premature cracking, surface distress and loss of traffic load-bearing capacity.
The paving contractor must take many variables into consideration to ensure that the asphalt mix is compacted to an acceptable standard. Some of these variables are controllable, and some are not. For instance, the temperature of the mix as it exits under the paver’s screed is critical for successful compaction. The temperature must be kept as high as possible to prevent the mix from cooling too quickly. The optimum temperature ranges from about 275deg F to 300deg F, depending on the type of asphalt mix and its characteristics.
As the mixture cools it becomes stiffer and harder to compact, which is why the contractor must work as fast as possible. In addition, the number of roller passes must be consistent and as close to continuous as possible. Rollers can be of any type, but the most common are breakdown steel wheel vibratory and pneumatic tire rollers. The rolling pattern used and the number of passes are determined by the governing specifications of the project.
Another factor that is directly related to the ability of an asphalt mixture to be compacted is the air void content. It is inversely proportional to density and the more voids in an HMA mixture, the lower the density and the weaker the pavement structure. A mix that is designed with a low air void content can be easily compacted to a very dense pavement.
Moisture damage is a major concern on all pavements, but especially in asphalt. This problem is caused by water entering the mixture between the asphalt coating on the aggregate and the loose particles. The degree of moisture damage is primarily determined by the gradation of the aggregate, but it is also affected by the amount of air voids in an asphalt mix. This is why it is important to keep the air void content in the mix below 8%.
Curing
The curing of asphalt is a critical step in the process of establishing a strong and durable pavement surface. It involves a chemical reaction that helps the oils in the asphalt to fully harden, allowing it to better handle wear and tear. However, it’s important to keep in mind that the duration of this stage varies depending on various factors, such as weather conditions and the unique composition of the asphalt mixture used in your project. Consequently, a good asphalt contractor will carefully manage these conditions to guarantee that your newly paved asphalt undergoes an ideal drying process and cures properly.
The temperature of the surrounding area plays a crucial role in the curing process. Warmer temperatures accelerate the asphalt’s curing, while colder ones slow it down. Additionally, the amount of humidity in the air also impacts this time. High humidity levels hinder the evaporation of moisture from the asphalt, resulting in longer drying periods than what would be expected under ideal conditions.
For this reason, asphalt contractors should always check the weather forecast before starting a paving job. They should avoid laying asphalt during rainstorms, as the excessive water can interfere with the chemical reactions that help the asphalt to harden.
In addition, it’s vital to restrict traffic on the new asphalt until it dries and cures properly. Rushing to use it too soon can cause ruts and depressions, which compromise the strength and durability of the pavement. It’s advisable to wait at least 24 hours before permitting light traffic and up to a week for heavy vehicles.
Fortunately, there are some methods you can employ to expedite the asphalt curing process and ensure it reaches its full potential. Some of these techniques involve the use of special curing agents that can be sprayed onto the fresh asphalt immediately after it’s laid. These agents create a moisture barrier, thereby helping the asphalt to dry more quickly and strengthen more effectively.
Another effective way to speed up the curing process is by spraying the asphalt with water containing an emulsifier. These substances combine oil and water, allowing the water to evaporate slowly from the surface while simultaneously enhancing the asphalt’s strength and durability.